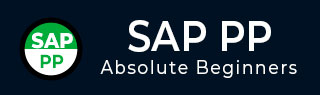
- SAP PP Tutorial
- SAP PP - Home
- SAP PP - Introduction
- SAP PP - Common Tables
- SAP PP - Organization Structure
- Integration with Other Modules
- SAP PP - Master Data
- SAP PP - Bill of Materials
- SAP PP - Work Center
- SAP PP - Routing
- SAP PP - Demand Management
- SAP PP - Creating PIR
- Material Requirement Planning
- SAP PP - MRP List
- SAP PP - Long Term Planning
- SAP PP - Production Orders
- SAP PP - Production Order Change
- Production Order Confirmation
- Canceling Production Order
- SAP PP - Capacity Planning
- SAP PP - Capacity Leveling
- SAP PP - Goods Receipt
- SAP PP - Stock Overview
- SAP PP - Goods Issue
- SAP PP - Goods Issue Reversal
- SAP PP - Lean Manufacturing
- SAP PP - Reports
- SAP PP - Material Document List
- Stock of Multiple Materials
- List in Bill of Material
- SAP PP Useful Resources
- SAP PP - Questions Answers
- SAP PP - Quick Guide
- SAP PP - Useful Resources
- SAP PP - Discussion
- Selected Reading
- UPSC IAS Exams Notes
- Developer's Best Practices
- Questions and Answers
- Effective Resume Writing
- HR Interview Questions
- Computer Glossary
- Who is Who
SAP PP Interview Questions
Dear readers, these SAP PP Interview Questions have been designed specially to get you acquainted with the nature of questions you may encounter during your interview for the subject of SAP PP. As per my experience good interviewers hardly plan to ask any particular question during your interview, normally questions start with some basic concept of the subject and later they continue based on further discussion and what you answer −
SAP Production Planning is one of key module in ERP and deals with planning processes like capacity planning and material planning and execution of production order, bill of material and goods movement. SAP PP module handles master data that is required for BOMs activity, work center and routing and keep it in a separate component.
Discrete production is known as industry where produce materials changed with each lot and costs are calculated as per orders and lots.
In Repetitive production, product is not changed for longer time period and production is done as total quantity and not in the form of individual lots.
Converting planned order to Production Order
First step is to convert a planned order to production order. When you create a Production Order, type is defined in SAP PP system.
Issue the production order
To start the production process, it is necessary to issue Production order. Till a production order is not released, execution of production process is not started.
Issuing goods for production order
Issuing goods is required for providing the goods to execute the Production order. Once goods are issues, document number can be updated in the system.
Production order confirmation
All the sub processes are executed in accordance with required operations to confirm the production as per Production order.
Good receipts w.r.t Production Order
Once production order execution is completed, goods produced w.r.t Production Order are received and placed in storage area.
In SAP PP module, organization structure defined the location of manufacturing plants and storage locations within the plant. At the top you have company and company code and then each company code contains different plant and storage locations.
To perform Production Planning and Control activities, SAP PP is closely integrated with other SAP ERP modules: SAP Sales and Distribution SD, SAP Material Management MM, Quality Management, Finance Accounting and Project System.
You can find list of below activities from Production Planning that are related to other SAP modules and integration with other modules.
SAP PP and SAP Material Management MM
- This involved movement of goods, auto goods receipt.
- It includes creating reservation for Production Order/Planning.
- Raising Purchase orders with MRP Run.
- Quotations and Vendor selection.
SAP PP and SAP SD
- This is used to check the availability of material for production order.
- To perform MRP Run, Requirement Types.
- Bill of Material components and operation.
SAP PP and SAP FICO
- Updating price in material master data
- Defining activity Type in the Cost center
- Assigning activity type to Work Center
- Cost Estimation
- Production cost controlling
- Posting accounting activities related to goods movement, material request, etc.
SAP PP and Project System
Assigning planning activities to WBS in the Project.
Running Material requirement planning at Project level (MD51). The procured material attached to WBS are reserved as project stock against the particular project.
The component attached to network are planned at plant level and are reserved as plant stock.
SAP PP and Quality Management
- Inspection Type 03 for discrete and repetitive manufacturing.
- Inspection Type 04 for both Discrete and Repetitive Manufacturing
- Bills of Material BOM
- Material Master
- Work Center
- Routing
Bill of material master data is related to material requirement planning and provides the list of components to produce the product.
To produce a product with different variants, you can create super Bills of Material that has list of components to manufacture different variants of a product and selection of component depends on details mentioned in planning order.
Material BOM
When a Bill of Material is created for a material is known as a material BOM in the SAP. Material BOMs are mainly used to represent the structure of products manufactured within your company.
Sales order BOM
Sales Order BOM is used when you specially tailor the make-to-order production of products as per requirements of the customers. To meet the customer requirements, you make sales order specific modifications to various assemblies.
You can create Bill of Material as single level or multiple level.
BOM type depends on the size, validity dates and production method.
You can create up to 99 Bills of Material as per material type.
You can use material Bill of material for the material available in PP module and equipment Bill of Material are used in Plant Maintenance module.
As mentioned you can create super BOM for different variants of a product.
Work center consists of master data related routing of products. It contains data related to scheduling, capacity planning and production costing.
All the manufacturing activities are performed in Work Center. Work center can be used to monitor these activities −
Scheduling
You can schedule the operations in Production order as per operating times in Routing and formulas mentioned in work center.
Production Costing
You can also check production costing as per formulas mentioned in work center. A Work center is also linked to cost center and it defines the cost of operation in Production Order.
Capacity Planning
You can find current capacity and future capacity requirements stored in work center.
Routine defines the list of activities to be performed for production process. Routing defines sequence of activities performed at work center. Routing plays in important role in calculating production cost, machine time and labor time.
To create routing it is mandate that you first define work center.
Multiple material can follow single routing group.
Routing is used for scheduling and costing of operation for raw and finished products.
Routing is used for calculation operation cost for finished product.
Make to Stock Planning strategy
This is planning strategy where stock is produced without sales order. It is used to meet customer demands in future.
When you use Planning strategy 10, only PIR quantity is considered for MRP run and sales order are completely ignored. In this PIR requirement type LSF and is reduced when you deliver stock to customer.
When you use Planning strategy 40, for MRP run maximum of 2 PIR and Sales order can be considered and PIR is reduced when enter the Sales order. PIR requirement type is VSF in this case.
Make to Order planning strategy
In this planning strategy, finish products are not produced until you receive sales order from a customer. For MRP run, you only consider Sales order.
In MTO strategy, you only produce sales order stock and products are delivered as per sales orders from specific customer.
You use Planning strategy 20 for make to order MTO process and planning strategy 25 is used to produce product variants when there is request for variant products from customer.
MRP run or planning run is an engine which is used to fill demand and supply gap. Issues & Receipts are called MRP Elements. Issues include PIRs, Dependent Requirements, Order Reservations, Sales Orders, Issuing Stock Transfer Orders, etc. and receipts include Production Orders, Purchase Requisitions, Purchase Orders, Open Production Orders, Receiving Stock Transfer Order, Schedule lines, etc.
MRP parameters are required to run material requirement planning to meet Planned Independent Requirement PIR and to use Routing information. Different MRP parameters can be used −
Processing Key
NetChange −
In this run system consider those material which has undergone some changes from the previous MRP run.
NetChange in planning horizon −
This run considers the requirement in predefined planning horizon and not like net change which check the future requirements.
In this run, system consider only those material which has undergone some changes from their last MRP run.
Regenerative Planning −
In this run, system consider all the material irrespective of changes and it is time consuming and not common in Production planning.
Scheduling
Basic Scheduling −
It only calculates basic dates for orders in MRP run and in house production time for material master in use.
Lead time Scheduling −
In this MRP, production dates are defined by lead time scheduling for planned orders.
Yes, by changing the configuration in OPL8- Order type dependent parameters as routing optional. When we try to create an order using C001 it may ask for a sales order.
Long term planning in SAP PP is used to check future demands at all Bill of Material level. You can check the current capacity and vendor ability to provide the material in required time period.
This is not actual run but is used to see if all capacity requirement can be fulfilled and you can also transfer simulative area to operative area if requirements are fulfilled.
Also note that it is not necessary that you perform simulative planning in long duration, it can be for short term and there is no time restriction.
A Production order is used to define the material to be produced, plant location where production has to be done, date and time of production, quantity of goods required. A Production Order also defines which components and sequence of operations are to be used and how the order costs are to be settled.
BOM and routing data of the materials are copied into the production order which determines the list of components and operational data in the order.
First step is to convert a planned order to production order. When you create a Production Order, type is defined in SAP PP system.
To start the production process, it is necessary to issue Production order. Till a production order is not released, execution of production process is not started.
Issuing goods is required for providing the goods to execute the Production order. Once goods are issues, document number can be updated in the system.
All the sub processes are executed in accordance with required operations to confirm the production as per Production order.
A Production Order can be created in following ways −
Directly from Stock Requirement List
Using Planned Order number
Capacity Planning is done to balance the load at work center and you can calculate production capacity based on requirement of product as per available capacity.
Capacity leveling is performed for performing detailed production planning purpose. This is done through planning table which is used to carry detailed planning of capacity requirements over time in future.
You can perform Capacity Leveling using Planning table and orders are processed as define in work center to meet the Production process.
To perform Capacity leveling, use T-Code: CM21
Good receipt is performed when material is produced as per Production order and goods is placed at storage location. The stock quantity is increased and movement type 101 is entered.
Use T-code: MIGO
Planned order are offset by production order and you can see the planned order details in the Production order.
In SAP PP, goods issue is done when raw material is consumed to produce material as per Production order. When goods are issued, system decreases the inventory of components at the storage location in Production Planning system.
Movement type 261 is used for goods issue.
To perform goods issue, use T-code: MB1A or go to Logistics → Production → Production Control → Goods Movement → Goods Issue.
Enter Movement type 261 for goods issue.
Goods issue reversal is used when you cancel the goods issue for an order. Goods issue can be cancelled till order status is confirmed CNF in system.
Movement type is 262 in Goods issue reversal.
You can use Stock overview to check the available stock at any point of time. Stock overview can be checked using T-Code: MMBE
MRP Controller is an individual or group of persons who are responsible to check material availability.
Planning horizon is used to define the period for the Net change planning in the planning horizon.
Before Production Order creation, you have to define Order Types, dependent parameters, backorder scheduling, and level.
MD04
This is used for Stock / Requirement list this is dynamic list which reflects even any small change is made in Master Data, Planned Order & Production order etc. for respective material for which you have executed stock / requirement list.
MD05 is used to view MRP list which displays results of last MRP run for the material for which you have executed MRP list.
SAP PP-PI provides an integrated planning tool for batch-oriented process manufacturing and is used in pharmaceutical, food and chemical industry to support planning of production, waste disposal in the plant.
You can check this in CO02 select Cost → Analysis and you can check the cost of Production Order.
Plan Cost = Planned Quantity X Planned Price
Actual Cost = Actual Quantity X Actual Price
Target Cost = Actual Quantity X Planned Price
SOP is forecasting tool that allows you to set the sales, production, and other supply chain targets based on existing, future, or historical data. SOP is most commonly used for finished goods.
SPO consists of following two components −
Standard SPO it is predefined in the system.
Flexible SOP You can configure it in multiple ways.
Use T-code: CO13
Enter order number and click on tick mark at the top. You will be prompted to confirm the action.
Capacity Planning is done to balance the load at work center and you can calculate production capacity based on requirement of product as per available capacity.
You need to check capacity load on work center and if any work center is overloaded, we need to move orders to different work centers.
To check Capacity Loads
Use T-Code CM01 or go to Logistics → Production → Capacity Planning → Evaluation → Work Center View → Load.
MAST Material BOM
STKO BOM Header
STOP BOM Positions
SAP Quality Management is part of SAP R/3 system and is integrated with other SAP modules like SAP Material Management MM, Production Planning PP and Plant Maintenance. QM is integral part of logistic management and is used to perform quality functions at incoming material, in process manufacturing process and raw material as well in the facility.
Inspection Type 03 for discrete and repetitive manufacturing.
Inspection Type 04 for both Discrete and Repetitive Manufacturing.
You can create up to 99 Bills of Material.
Material staging is called when you transfer the material from your main store to production location.
This is used to record work process in the system and to get the requirements of repetitive, mass or flow manufacturing.
Stock transfer This is known as the transfer of stock for the usage in the same company.
Stock transport This is known as change of title of stock in the name of the buyer.
Work Center
Routing
You want to change the details in Production Order, you can do this by using below code.
Use T-code: CO02
To display the Production Order, T-code: C003
For Material Requirement Planning MRP −
Table | Description |
---|---|
MDKP | Document Header data |
MDTB | Table Structure |
MDVM | Planning File Details |
MDFD | MRP Date details |
S094 | Stock Analysis |
For Repetitive Manufacturing −
Table | Description |
---|---|
S025 | Run Schedule Quantities |
S026 | Material Usage |
S028 | Reporting Point Statistics |
SAFK | RS Header Master Data |
What is Next?
Further you can go through your past assignments you have done with the subject and make sure you are able to speak confidently on them. If you are fresher then interviewer does not expect you will answer very complex questions, rather you have to make your basics concepts very strong.
Second it really doesn't matter much if you could not answer few questions but it matters that whatever you answered, you must have answered with confidence. So just feel confident during your interview. We at tutorialspoint wish you best luck to have a good interviewer and all the very best for your future endeavor. Cheers :-)