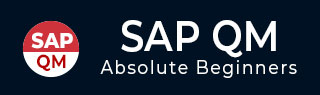
- SAP QM Tutorial
- SAP QM - Home
- SAP QM - Overview
- SAP QM - Components
- SAP QM - Integration
- SAP QM - Master Data
- SAP QM - Inspection Methods
- SAP QM - Sampling
- SAP QM - Inspection Plan
- SAP QM - Quality Info Records
- SAP QM - Lot Inspection
- SAP QM - Result Recording
- SAP QM - Usage Decision
- SAP QM - Listing Inspection Lot
- SAP QM - In-Process Inspection
- SAP QM - Final Inspection
- SAP QM - Defects Recording
- SAP QM - Quality Notification
- SAP QM - Benefits
- SAP QM - Tables
- Consultant Responsibilities
- SAP QM Useful Resources
- SAP QM - Questions Answers
- SAP QM - Quick Guide
- SAP QM - Useful Resources
- SAP QM - Discussion
- Selected Reading
- UPSC IAS Exams Notes
- Developer's Best Practices
- Questions and Answers
- Effective Resume Writing
- HR Interview Questions
- Computer Glossary
- Who is Who
SAP QM Interview Questions
Dear readers, these SAP QM Interview Questions have been designed specially to get you acquainted with the nature of questions you may encounter during your interview for the subject of SAP QM. As per my experience good interviewers hardly plan to ask any particular question during your interview, normally questions start with some basic concept of the subject and later they continue based on further discussion and what you answer −
SAP Quality Management is part of SAP R/3 system and is integrated with other SAP modules like SAP Material Management MM, Production Planning PP and Plant Maintenance. QM is integral part of logistic management and is used to perform quality functions at incoming material, in process manufacturing process and raw material as well in the facility.
- Quality Planning
- Quality Notifications
- Quality Inspection
Quality planning allows to plan the inspection of goods from the vendor, raw material, work in process and final product.
Quality notification includes the defect identification and steps to be taken by quality department.
Inspection plan definition is an important part of the QM planning process. The inspection plan contains the number of characteristics of the item are to be inspected and list of tests to be performed for performing the inspection.
Under Quality assurance, it includes the quality inspection.
A Quality inspection involves someone from the quality department inspects an item as per defined points in inspection plan. You perform the inspection based on one or more inspection lots, where a lot is a request to inspect a specific item.
In SAP system, you can create Inspection lot either manually by a user or automatically in the system.
Under quality control, you have quality notifications, standard reports and Quality notification system. What actions has to be taken as per defect finding.
The quality notification process includes recording problem that is either identified by a customer for a product manufactured in an organization, or in a company against the product of a supplier/vendor.
Quality notification can be raised internally to raise an issue that has arisen on the production line. A quality notification can be assigned to an existing order or you can also create a new order as per the quality notification.
You can create reports in QM system to check how many times a product has been identified with a defect and improvement areas that your company has to implement. There are number of reports that can be generated in QM −
Material Defects report
It can be used to check the number of times an item has been identified with a defect status.
Vendor Defect report
This report is used to show the number of defected material supplied by a vendor.
This can be checked by examining the inspection lots for goods receipts, a quality department can highlight vendors who are material which are failing in inspection.
Customer Defect report
This report is used to show the defects that were found on inspections for outbound deliveries. This helps organization to improve the quality of goods delivered and hence raise the customer satisfaction.
- SAP Material Management
- SAP Production Planning
- SAP Sales and Distribution
- SAP Controlling
You manage the quality details for materials, vendors and suppliers.
You manage the releases for vendors and manufacturers and also monitor QM systems for suppliers.
You manage the release status of delivery from vendor.
You can maintain quality agreements and RFP details when you request for a quotations and purchase orders is raised for vendors.
You can manage quality certificates for vendors.
Using SAP QM process, you can also initiate an inspection at supplier site before there is delivery due from the supplier.
You can integrate SAP QM with Sales and Distribution to perform the following activities −
You can manage quality information related to customer for sales and distribution process.
In SAP QM system, you can initiate an inspection when a delivery is created against a purchase order.
You can manage quality in sales & distribution by performing quality notifications and RCA’s and by processing customer complaints to improve customer satisfaction.
You can integrate SAP QM with PP to perform the inspection planning and work scheduling in SAP system.
As part of SAP quality management process, you handle inspection characteristics and also define characteristics for the operation.
You can manage quality inspections for manufacturing orders.
Using SAP QM, you can set up the final inspection from the goods receipt after production process is complete.
You can use QM process to manage partial lots of a material during production which are different in quality.
You can confirm the quality information as per manufacturing orders.
Using SAP QM, you can monitor the production quality with the help of control charts and reports in Production planning.
You can integrate SAP QM with controlling process to manage the costs for defect control and non-confirmative costs in production process.
You can directly get the results for quantitative specifications from inspection while doing result recording. You can set limits like minimum and maximum value for each parameter at master level. You can also attach the inspection method to inspection specification level.
These specifications can take values like true/false or OK/Not OK.
You can use inspection method to perform the inspection. An inspection method can be assigned to master inspection charactertics or directly to an inspection charactertics in an inspection plan.
An Inspection method can be created in one plant same method can be used in other plant.
Creating an Inspection method
To create an inspection method, use T-code: QS31.
Sampling procedure in QM is used to determine the size of inspection lot to be used in inspection plan under Quality planning. You can define a sampling procedure as fixed sample, percentage or other sample.
A collection of sampling plans. You use a sampling scheme if you want to −
Determine the sample size on the basis of the lot size, inspection severity, or combination of inspection severity and AQL (actual quality level)
Store how a decision is made to accept or reject a characteristic.
Determine the number of physical samples, based on the lot size, or the number of containers in an inspection lot in sample management.
The sampling type defines how a sample is calculated (for example, fixed sample, 100% inspection, use sampling scheme, percentage sample). Together with the valuation mode, the sampling type defines the parameters for sample determination.
Using the sampling type, the system proposes a list of rules for sample determination. If there is only one rule available, this is automatically chosen.
The valuation mode defines the rules for accepting or rejecting a characteristic or sample. The sampling type and the valuation mode specify which parameters the system uses to determine a sample size.
If you want to use inspection points in the sampling procedure, you need to set an indicator for the corresponding application area. This indicator specifies how many inspection points are to be created for each inspection lot.
If you want to use quality control charts in a sampling procedure, you must enter a quality control chart type. The control chart type specifies −
- The characteristics for which the control chart is suited
- The control variables a chart contains
- How the control limits are calculated
Sampling procedures can be referenced in task lists, material specifications and in the inspection setup. The where-used list displays the task lists, material specifications and inspection setup, in which a sampling procedure is used.
Maximum fraction of nonconforming units (as a percentage) or maximum number of defects per 100 units permitted for a lot to be accepted. The AQL (Acceptable Quality Level) is the quality level that represents the upper limit of a satisfactory average quality level for an acceptance sampling inspection.
Materials to be inspected.
How the inspection of materials need to be taken place.
What characteristics to be inspected, work center and inspection specifications.
In the inspection plan, you have to define the sequence of inspection steps to be performed and the range of specifications as per master inspection characteristics MIC, sampling procedure to calculate the sample size for inspection, inspection method, etc.
Quality info records are used to manage the supplier relation in an organization. When there is continuous defect in the material supplied by a vendor, you can use quality info records to block a vendor.
When you create a purchase order, SAP system performs a check to find if a Quality info record is required and is available for combination of material and vendor.
Quality information record has to be maintained when you use the source inspection functionality that means a material has to undergo an inspection prior to the material reaches the plant for Goods Receipt.
You can set under Quality Info record that inspection is required when it is procured from vendor A and is not required if you procure from Vendor B.
You can create sampling schemes −
For attributive inspections
For variable inspections based on the s-method
Without valuation parameters, if you use the sampling scheme in a sample-drawing procedure or in a sampling procedure that calls for a sample calculation without a task list
Depending on the valuation parameter used, the sampling plan consists of −
- The sample size, acceptance number, and rejection number for attributive inspections.
- The sample size and K-factor for variable inspections.
- The sample size if without valuation parameters was specified.
In SAP system, you can perform the incoming inspection for different material like raw material inspection, in progress material inspection or final goods inspection. Good receipt is generated as part of purchasing or against a scheduling agreement.
For each good receipt, SAP system creates a one inspection lot which contains details- vendor, date or purchase, etc.
You can do the result recording for the inspection lot created at the time of Goods Receipt.
To perform the Result recording, go to T-code: QA32
Usage decision is used to decide whether you want to accept or reject the goods in the inspection lot based on the results of the inspection. As per inspection results the process is marked as completed.
To control QM activities, you can, for example, define the following −
- Procurement data
- Procurement control key
- Certificate type
- Requirements for the vendor's QM system
- Technical delivery terms
Display inspection setup −
- Inspection type
- Use of a task list or material specification
- Results recording for characteristics
- Quality score procedure
- Sample determination
Go to Logistics → Quality management → Quality planning → Logistics master data → Material → Inspection setup.
Choose "Activate insp. type" or "Deactivate insp. Type.
Yes, Example: Inspection in each shift, etc.
The in process inspection has a reference to a production order in SAP system. You generate an Inspection lot at the time of production order release and inspection type for in-process inspection is 03 in the system. When there is a production order release, inspection lot will be automatically created in the system.
You perform final inspection of goods after production goods receipt in SAP system. Inspection lot is created after goods receipt for a production order.
Inspection lot type is 4 for final inspection.
Inspection plan in SAP is normally a task list based high level object describing details about what characteristics must be tested in order to ensure the quality of the product.
Inspection method is detailed info describing how to carry out inspection. It is a separate object and can be assigned to either characteristic or in the plan directly.
Goods Receipt Inspection −
- Performed after receiving the goods
- Performed at receivers/customers place
- Goods receipt for purchase order triggers the inspection lot creation
- Inspection lot is created after receiving the goods
Source Inspection −
Performed before receiving the goods
Performed generally at suppliers place with customers participation
Quality info record triggers the inspection lot creation. To trigger the lot open purchase order required for the Material, Plant and vendor combination.
Inspection lot created before receiving the goods based on the lead time in Quality Info record. There is also option to create inspection lot after goods receipt.
Final inspection process consists of the following steps −
- Creation and Confirmation of Production order
- Listing Inspection lot
- Attaching and releasing inspection lot
- Sampling
- Result recording
- Usage decision
- Posting the stock
In SAP QM, you can capture different types of record which are identified at the time of inspection. SAP Quality notification can be used to analyze the defects identified and perform root cause analysis.
Complaints filed by customers
This includes the defects identified in goods that are delivered to customers. You can use standard SAP Quality notification Q1 to record customer complaint and take action against problem reported by customer.
Complaints identified in vendor delivered goods
This includes the defect identified with quality of goods delivered from supplier/vendor. You use standard SAP QM notification type Q2 to record a complaint against vendor and take action for the incoming material.
Internal Defects
This includes recording internal problems which are identified at the time of in process quality inspection. You use standard SAP QM notification type Q3 to deal with problems identified in goods manufactured in a company.
Quality notification you can record different type of problems occurred due to poor quality of goods. Quality notifications can be created for the following internal and external problems −
- Defect Analysis
- Customer Complaint
- Complaint against vendor
Use QC21- Quality Certificate
- Ordering Address OA
- Vendor VA
- Invoicing Party PI
Eight
- Customer Focus
- Leadership
- Process Approach
- Involvement of People
- System Approach to Management
- Continual Improvement
- Factual approach to decision making
- Mutually beneficial supplier relationship
Requirement type and requirement class are assign with planning strategy. Requirement type is only description but it is contend of requirement classes they control the creation and execution of PIR, Sale Order & Stock consumption.
SAP Quality management integration with other modules is one of the key aspect of quality management. You can implement the quality process in Material Management, Production planning and other SAP modules.
You can access to data maintained in the system related to customer, vendor and supplier master.
Using SAP QM, a standardize process can be implemented.
SAP Quality management process helps you to incorporate the improvement process - by monitoring the processes, defect identification and quality notifications.
You can perform automation of information flow by which inspection lot gets created automatically when you release the production order or goods receipt.
Using SAP quality management process, you can perform the quality compliance of raw materials when it is first delivered by vendors/suppliers and in process manufacturing and also after the production process is completed.
SAP QM also responsible to perform the compliance with customer’s quality specifications you ship the goods to customer as per Purchase order.
The ISO 9000 family of quality management systems standards is designed to help organizations ensure that they meet the needs of customers and other stakeholders while meeting statutory and regulatory requirements related to a product.
Vendor Defect report
This report is used to show the number of defected material supplied by a vendor.
This can be checked by examining the inspection lots for goods receipts, a quality department can highlight vendors who are material which are failing in inspection.
Customer Defect report
This report is used to show the defects that were found on inspections for outbound deliveries. This helps organization to improve the quality of goods delivered and hence raise the customer satisfaction.
- Material
- Inspection lot creation date
- Batch
- Vendor
- Inspection dates
- Plant
- Inspection type
- QPAM Inspection catalog selected sets
- QPMK Inspection characteristic master
- QPMT Master Inspection Characteristics Texts
- QPMZ Master Inspection charactertics MIC
- QMAT Inspection type for material parameters
- QMHU shows QM link in Inspection lot and handling unit Item
- QMTB Inspection method master record
- QMTT Inspection Method texts
- QPAC Inspection catalog codes
What is Next?
Further you can go through your past assignments you have done with the subject and make sure you are able to speak confidently on them. If you are fresher then interviewer does not expect you will answer very complex questions, rather you have to make your basics concepts very strong.
Second it really doesn't matter much if you could not answer few questions but it matters that whatever you answered, you must have answered with confidence. So just feel confident during your interview. We at tutorialspoint wish you best luck to have a good interviewer and all the very best for your future endeavor. Cheers :-)